Papierlose Fertigung
mit Losgröße 1 in der Produktion.
In der Initiative zur Realisierung einer „Paperless Factory mit Losgröße 1“ hat die Tischlerei Grömmer in Zusammenarbeit mit Zentro neue Standards für die Digitalisierung in der Tischlerindustrie gesetzt. Nach Abschluss des Projekts verarbeitet das Unternehmen Aufträge auch bei Einzelstückfertigung vollständig digital. Das von Zentro implementierte Produktionsleitsystem Zentro Go erleichtert dabei durch effiziente Kommunikationswege, präzise Einzelteilverfolgung und optimiertes Qualitätsmanagement die Prozesse des Teams bis zur Montage.
Im Einklang mit dieser digitalen Transformation gewährleistet das System von Zentro die nahtlose Integration von Stücklisten und Produktionsdaten mit dem ERP, der Kapazitätsplanung sowie den Maschinen, was essenziell für die Aufrechterhaltung einer hohen und gleichbleibenden Produktivität in der Projektumsetzung ist.
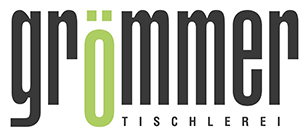
Paperless Factory.
“Wir waren lange auf der Suche nach einer Lösung, die unsere Ansprüche hinsichtlich Innovation, Flexibilität, Transparenz und Einfachheit in der Bedienung abdecken kann. Zentro Go konnte unsere individuelle Anforderung zu 100 % erfüllen.”
Konrad Grömmer
Geschäftsführer, Tischlerei Grömmer
Steigerung der Produktionseffizienz durch
Paperless Factory.
Bei der Tischlerei Grömmer zielte das ‚Paperless Factory‘-Projekt auf die Reduktion des nicht-wertschöpfenden Zeitaufwandes von 70 %, der hauptsächlich in administrativen Tätigkeiten besteht. Die Einführung dieser Strategie erfolgte durch das softwaregestützte System Zentro Go, das speziell für das Management von Einzelfertigungen konzipiert und integriert wurde. Dieses System vereint Funktionen zur digitalen Kommunikation, Prozessdokumentation, automatisierten Planung sowie Qualitätssicherung und verbindet sich nahtlos mit vorhandenen IT-Ressourcen, was eine deutliche Optimierung der Arbeitsprozesse ermöglichte.
Nach der Implementierung verzeichnete die Tischlerei bereits innerhalb des ersten Monats eine beträchtliche Reduktion der Durchlaufzeiten, was die Positionierung als innovatives Unternehmen im Markt signifikant stärkte.
Innerhalb eines Jahres gelang es, die Digitalisierungslücken zu schließen und somit auf bestehenden Leistungen aufzubauen.
Effizienz
"Mit Zentro Go brauchen wir nicht mehr lange suchen. Jeder weiß sofort, was zu tun ist."
Andrea
vom Team Grömmer

Vorgehensweise
In der Vorprojektphase wurde eine grobe Anforderungsanalyse auf Basis der vom Kunden zur Verfügung gestellten Informationen durchgeführt. Ausgehend von den Anforderungen wurde ein Grobkonzept erstellt und zur Gewährleistung höchstmöglicher Transparenz auch grafisch visualisiert. Das Grobkonzept diente als Grundlage für die Kostenschätzung und als Diskussionsgrundlage für die Spezifikation der zu implementierenden Lösung.
Bereits vor Projektbeginn entstand ein gegenseitiges Vertrauensverhältnis. Ein Mix aus bestehenden und neuen Softwaretools, Individualprogrammierungen und organisatorischen Maßnahmen wurde zu einer Gesamtlösung integriert. Dieser ganzheitliche Ansatz, der die Vorarbeiten des Kunden in allen betroffenen Bereichen berücksichtigte, qualifizierte die Lösung als ideale Wahl.
Vor Projektabschluss war eine mehrwöchige Probebetriebsphase mit festgelegtem Endtermin vorgesehen. Sie gab einerseits dem Kunden nach Abschluss der Implementierungsarbeiten die Möglichkeit, die Lösung mit einer breiten Anwendergruppe zu testen und auf eventuelle Änderungswünsche auch noch spät im Projekt einzugehen. Andererseits verhinderte die Deadline potenzielle Verzögerungen.
Durch das Projekt avancierte Grömmer zum Technologieführer der Branche im Bereich der papierlosen Fertigung. Diese ist für Losgröße 1, nach unserem Wissen, einzigartig im Tischlerhandwerk. Der Einsatz von KI im Rahmen der Lösung betont die Technologieführerschaft weiter. Die Umsetzung agiler Methoden in einem iterativen Prozess unterstreicht den innovativen Charakter des Projekts.
Zudem führte das Projekt zu einer Reduktion des Papierverbrauchs um etwa 90 %.
Transparenz
“Da es in der heutigen Zeit immer schwieriger wird, gut ausgebildetes Personal zu finden, sehen wir unsere Chance nur darin, die Produktivität unseres bestehenden Personals so hoch wie möglich zu halten und die Arbeitsweise sehr transparent und effizient zu gestalten.”
Konrad Grömmer
Geschäftsführer, Tischlerei Grömmer
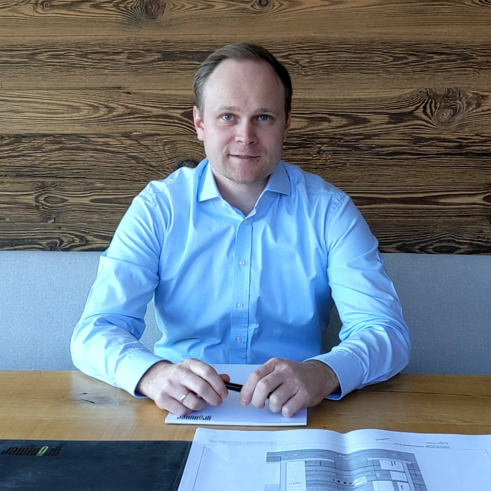
Qualifiziertes Personal
Die Bindung qualifizierter Mitarbeiter stellt aktuell eine der bedeutendsten Herausforderungen für Arbeitgeber dar. Die im Projekt realisierte, fortschrittliche Lösung leistet einen entscheidenden Beitrag zur Bindung von Schlüsselpersonal und gewährleistet nachhaltige Arbeitsplatzsicherheit für alle Qualifikationsniveaus.
Arbeitgeber stehen in der Verantwortung für ihr Team, insbesondere angesichts sozialer Herausforderungen und wachsendem Druck auf die Einzelnen. Durch die Einführung der neuen Lösung konnte die psychische Belastung am Arbeitsplatz verringert und das Risiko für Burn-out signifikant reduziert werden.
Darüber hinaus hat dieses Projekt den betrieblichen Handlungsspielraum unseres Kunden vergrößert, was sowohl zur Sicherung der bestehenden Arbeitsplätze beiträgt, als auch eine Expansion der Geschäftsaktivitäten erleichtert.